Pervaporation is an energy efficient combination of membrane permeation and evaporation. It's considered an attractive alternative to other separation methods for a variety of processes. Which can be used for breaking azeotropes, dehydration of solvents and other volatile organics, organic/organic separations such as ethanol or methanol removal, and wastewater purification.
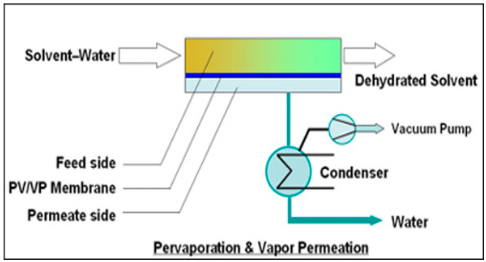
Pervaporation involves the separation of two or more components across a membrane by differing rates of diffusion through a thin layer and an evaporative phase change comparable to a simple flash step. A concentrate and vapor pressure gradient is used to allow one component to preferentially permeate across the membrane. A vacuum applied to the permeate side is coupled with the immediate condensation of the permeated vapors. Pervaporation is typically suited to separating a minor component of a liquid mixture, thus high selectivity through the membrane is essential.
High performance
Zeolite PV membranes have been successfully developed and applied in China since 2007. This new technology have been widely accepted in many industries like pharmaceutical, semi-conductivity, petrol chemical,etc. It have been prooved from many projects that PV&VP technology has many advantages than traditional dehydration processes like evaporation, distillation, and zeolite adoption.
Process Characteristics of PV/VP:
* Low energy consumption, less running cost
* No entrainer required, no contamination to product
* Easy operation and less maintenance
* Functions independent of vapor/liquid equilibrium
* Reliable treated solvent quality
* Less labor cost
* Less waste discharge
Solvent Dehydration by PV&VP Technology:
Over 300 industrial plants have been built in the past 10 years. Over 20 kinds of solvents have used membrane dehydration, such as methanol, ethanol, IPA, THF, acetonitrile, acetone, VOCs treatment,etc. The total capacity of industrial PV projects by Zeolite membranes in China is more than 2 million tons/a. The major applications are for pharmaceutical solvent recovery, bio-ethanol production, electrical solvent recovery and esterification reaction enhancement. This PV &VP technology will surely see more market in the future in process industry.
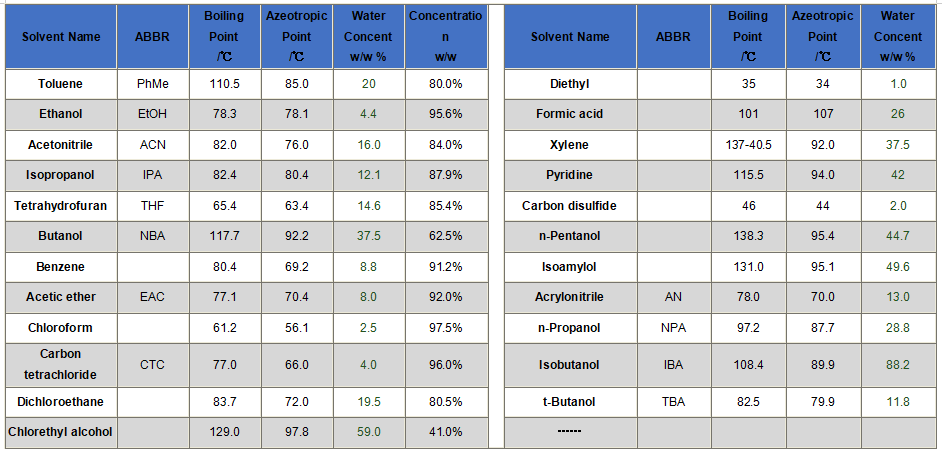
Ethanol is widely used as bio-energy and solvent. The azeotrope of ethanol/water (94.6/4.4wt%)
makes the dehydration process complex and energy consuming by traditional processes. The pervaporation makes the dehydration of ethanol simple and easy. The lowest water content of dehydrated EtOH after membrane process can be less than 0.05wt%.
For dehydration of ethanol, the comparison of OPEX and CAPEX for pervaporation and traditional technologies is listed as following project basis:
Feed condition: Ethanol 90% water 10%
Feed Capacity: 10000t/a (1250kg/h)
Product EtOH purity: 99.5%
Unit: /ton product IPA
.png)
IPA Dehydration by Zeolite Membranes
Isopropanol is widely used as solvent and disinfector. It’s most used solvent in pharmaceutical industry
such as antibiotic medicine production. The azeotrope of IPA/water (87.4/12.6wt%) makes the dehydration process complex and energy consuming by traditional processes. The pervaporation makes the dehydration of ethanol simple and easy.
For dehydration of IPA, the comparison of OPEX and CAPEX for pervaporation and traditional technologies is listed as following project basis:
Feed condition: IPA 85% ,water 15%
Feed Capacity: 10000t/a (1250kg/h)
Product IPA purity: 99.5%
Unit: /ton product IPA
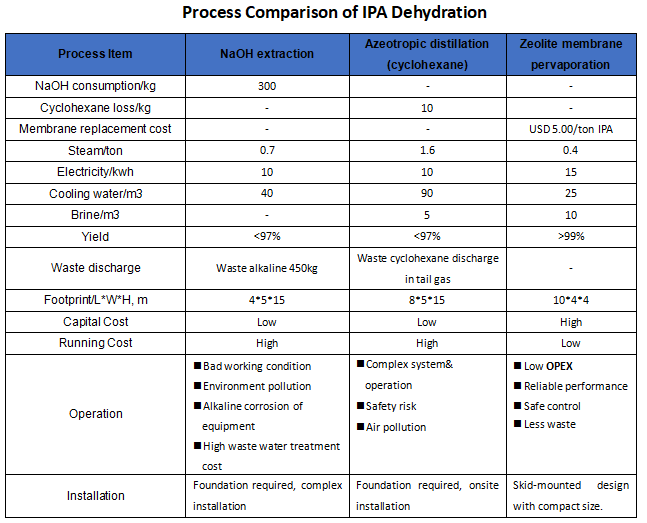
THF Dehydration by Zeolite Membranes
THF is a widely used solvent in pharmaceutical industries, typically used in antibiotic medicine production and Grignard Reaction. It forms azeotrope with water (95/5wt%) while the recovery of THF solvent requires water content of 0.03~0.5wt%. Traditional technologies usually use differential pressure distillation or extractive distillation, which is highly energy consuming, low efficiency. It’s also dangerous to distill THF since it can easily form peroxide during the process which is highly explosive. Pervaporation makes the dehydration of THF simple and easy, and safe. Despite of different product water content (from 0.01~1%), the energy consumption remains similar by only using different membrane areas.
For dehydration of THF, the comparison of OPEX and CAPEX for pervaporation and traditional technologies is listed as following project basis:
Feed condition: THF 95% ,water 5%
Capacity: 10000t/a (1250kg/h)
Product THF purity: 99.95%
Unit: /ton product THF